Pallet-compatible packaging development with MultiPack
With MultiPack, you quickly and reliably calculate pallet-compatible packaging solutions for products, outer packaging and/or transport packaging, for a large range of product geometries. The user inputs the packaging requirements and in a matter of seconds, the intuitive and high-performance analysis and planning tool for the packaging development delivers proposed solutions for the best possible utilization of the storage space on the pallet. It also makes further suggestions which can be interesting alternative options for the user. MultiPack offers numerous powerful functions which guarantee a close-to-reality, detailed visualization of all analyzed solutions so that the user can accurately evaluate them. Many customers achieve impressive additional benefits from the integration of custom add-ons, which can also be implemented retrospectively. Our customers benefit from free, non-time-limited corrective maintenance of the standard software as well as expert support by phone, e-mail or TeamViewer. You too can save time and money by using MultiPack for your packaging development and palletization planning. Would you like to test a (time-limited) full version of MultiPack free of charge? Simply contact us using the contact form or by e-mail to info@multiscience.de. Or briefly tell us what you need. We’ll be happy to help you.
The MultiPack two-stage analysis module used by our customers for the packaging development maximizes the number of products per pallet by focusing on the product packaging and outer packaging on the pallet. The user controls the interactive analysis and planning process by determining the parameters to be varied. These can be for example the dimensions, quantity, vertical orientation, and/or arrangement of individual packs inside the outer packaging. Based on the user’s specifications and in a matter of seconds, MultiPack’s optimization algorithms calculate one or more pallet-compatible dimensions of the product packaging and/or outer packaging. If you use standard packagings, the system selects one or more optimal standard packaging variants. The module also provides further possible solutions which can be interesting alternative options.
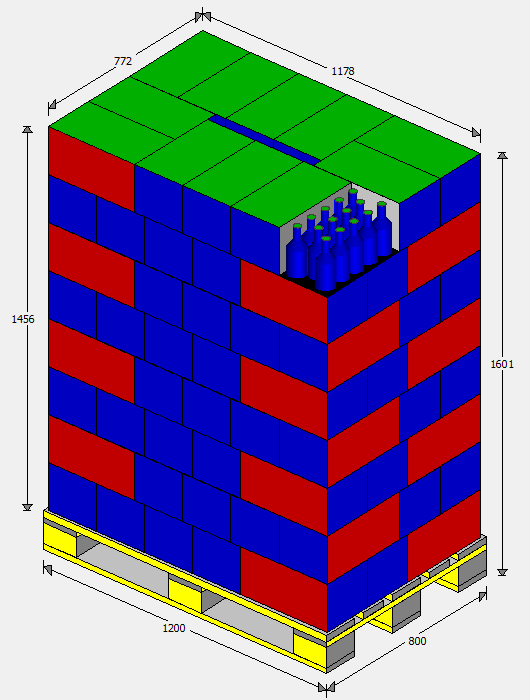
Two-stage analysis by MultiPack: Stowage plan with optimized outer packaging
The three-stage analysis by MultiPack used by our customers optimizes product packaging, outer packaging and transport packaging on the pallet in order to maximize the number of products per pallet. With this function, the user can vary the quantity, the vertical orientation and/or the arrangement of the outer packages in the transport packaging. The user can also specify standard packaging for the transport packaging. Based on the customer’s requirements, our MultiPack optimization algorithms take just seconds to find optimal packaging solutions for individual packaging, outer packaging and/or transport packaging. That means maximizing the number of products per pallet. Due to the complexity of the optimization task, Multiscience is the only supplier that offers a three-stage analysis.
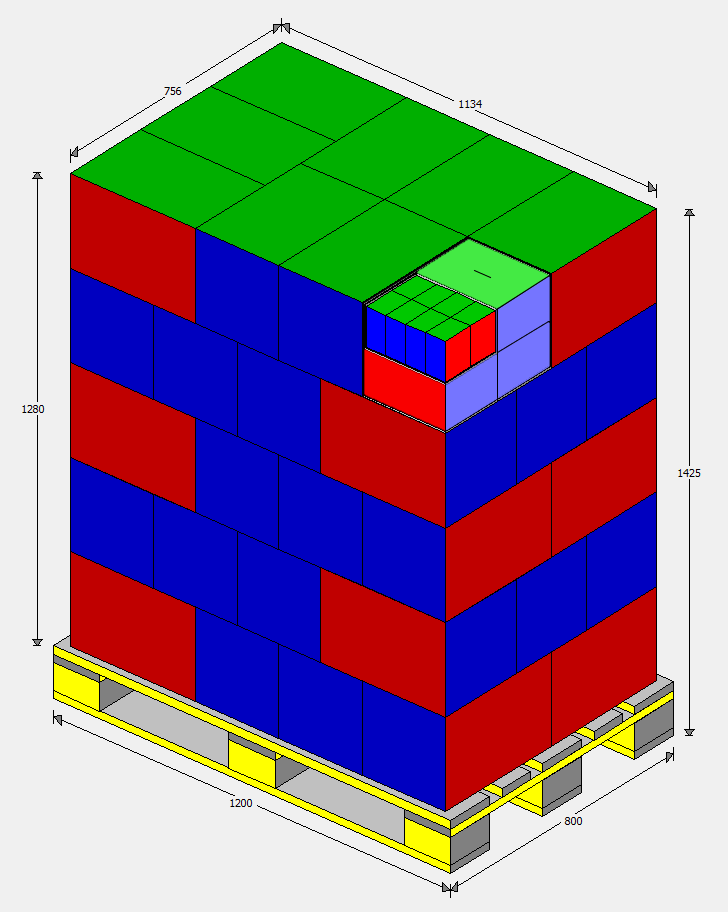
Three-stage analysis by MultiPack: Stowage plan with optimized outer packaging and/or optimized transport packaging
Outer packaging for various product geometries dimensioned for optimum pallet space utilization…
Optimal packaging development with the two-stage analysis: Overview
Based on the concrete situation of the user in the packaging development and the available design options, MultiPack’s two-stage analysis for individual or outer packaging calculates suggested solutions for best-possible pallet utilization. This means solutions with the maximum number of products per pallet as well as other suggestions which may be interesting alternative options for the user.
MultiPack can for example optimize the dimensions of the individual package. However, in most situations these dimensions are fixed. Therefore, if the use of the storage space on the pallet is unsatisfactory, the user can analyze other options to achieve pallet-compatible outer packaging. If, instead of using customized outer packaging, the user wants to choose a standard packaging from the available range, the MultiPack optimization algorithms determine the standard packaging(s) that ensure best utilization of the pallet. As we will show in further examples, the user can choose e.g. a different vertical orientation, an alternative arrangement or a different number of product packages in the outer packaging to achieve significantly better pallet utilization. Sometimes merely choosing not to palletize the outer packagings in layers can produce the best possible use of the storage space on the pallet. Here again, the MultiPack optimization algorithms offer alternatives that can help solve the problem.
The user controls the 2-stage MultiPack analysis by specifying what analysis parameters should be varied, either on their own or together with other parameters. To help the user evaluate the suggested solutions, which are generated in a matter of seconds, MultiPack includes a large number of powerful functions that provide realistic, detailed visualizations of each suggested solution. The interactive analysis and planning process controlled by the user according to the specific requirements of the case results in an outer packaging which is in his view ideally tailored to the product and the pallet.
Simple data entry for product and outer packaging
Intuitive dialog windows are used to enter the data on the product packaging, outer packaging, and pallet. In the example shown here, the user is planning a solution for a new product with the external dimensions 90 x 60 x 110 mm. He wants to know how many products per outer packaging would ensure the best use of storage space on the pallet if the outer packaging contains between 8 and 12 rectangular products in a single-layer pattern. Because the product can only be placed vertically by height in the outer packaging, only two of the six possible orientations are permitted.
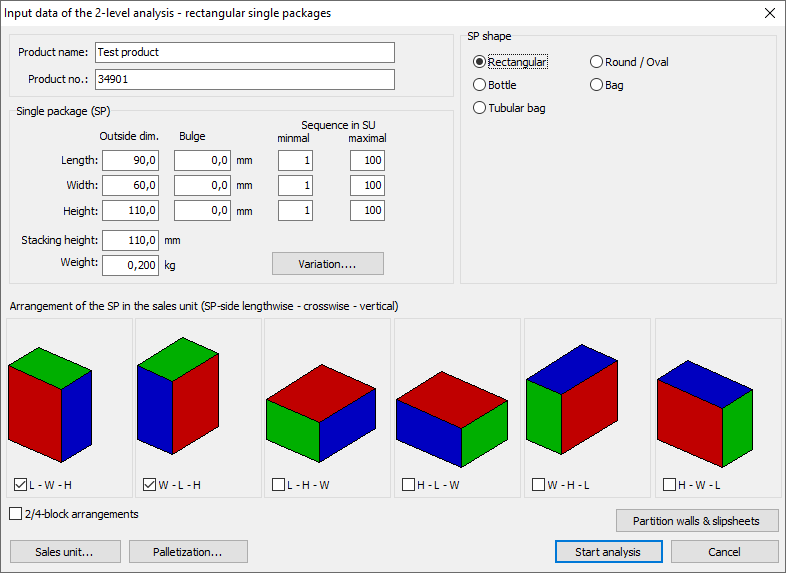
MultiPack two-stage analysis: Input window for rectangular individual packagings
The input window for the outer packaging displays all the options calculated by MultiPack for selection of the outer packaging. In this example, the user has decided on a tailor-made outer carton with FEFCO code 0201 and material thickness 3mm. The user enters the dimensioning requirements in the input boxes at the bottom of the screen. The permitted number of product packagings per outer packaging is specified here as 8 to 12.
As an alternative to a tailor-made outer packaging, the user can specify that an optimal standard packaging from the available range or a specific packaging must be chosen.
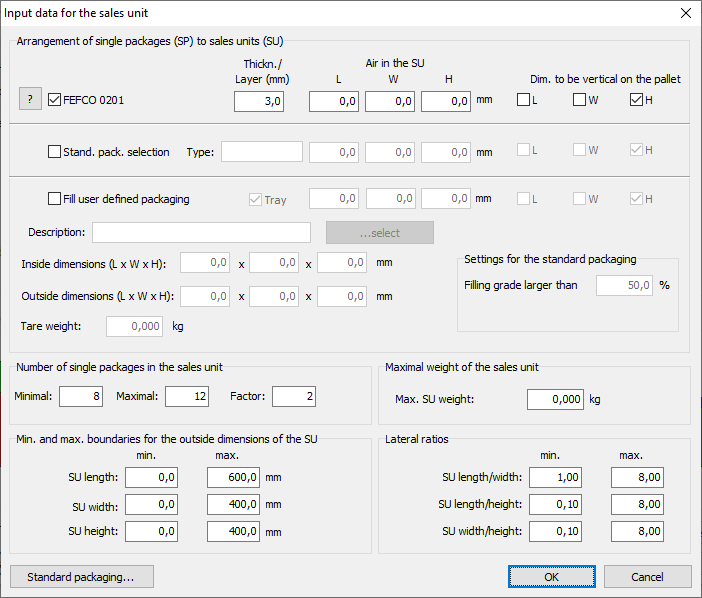
MultiPack two-stage analysis: Input window for outer packaging
In the adjacent input window, the user enters and usually saves the requirements for palletization of the outer packagings. These are: the pallet dimensions, the usable stowage space, the palletization type (in layers or not in layers), weight limits.
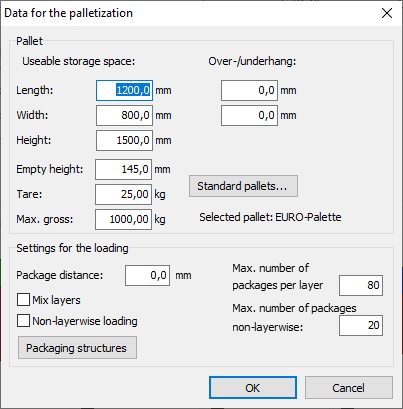
MultiPack two-stage analysis: Input window for palletization
Structured overview of the solution alternatives
Depending on the scope of the packaging development task, the MultiPack optimization algorithms calculate in fractions of a second up to 400 solution suggestions and present them in a solution report.
The easy-to-read solution report shows
- at the top left the highest-ranking suggested solutions, which are ordered according to the number of products per pallet in descending order
- at the bottom left details of the highlighted solution including the dimensions of the individual packaging and outer packaging, plus a 3D graphic of the arrangement of the individual packagings inside the outer packaging
- information about the space and volume utilization of the pallet for the highlighted solution
- on the right a 3D visualization of the pallet stowage plan for the highlighted solution with the best stacking solution, if composite stacking is possible.
The solution report gives the user initial information he needs to choose a solution: Based on the specifications entered in the input dialog, the report presents the best space utilization for the pallet using a tailor-made outer packaging with 10 individual packagings: 1,920 products per pallet. Under list Nos. 2 to 5, the report states the optimal dimensioning of the outer packagings with 8, 9 and 12 products as well as how many products can be placed on the pallet in each case.
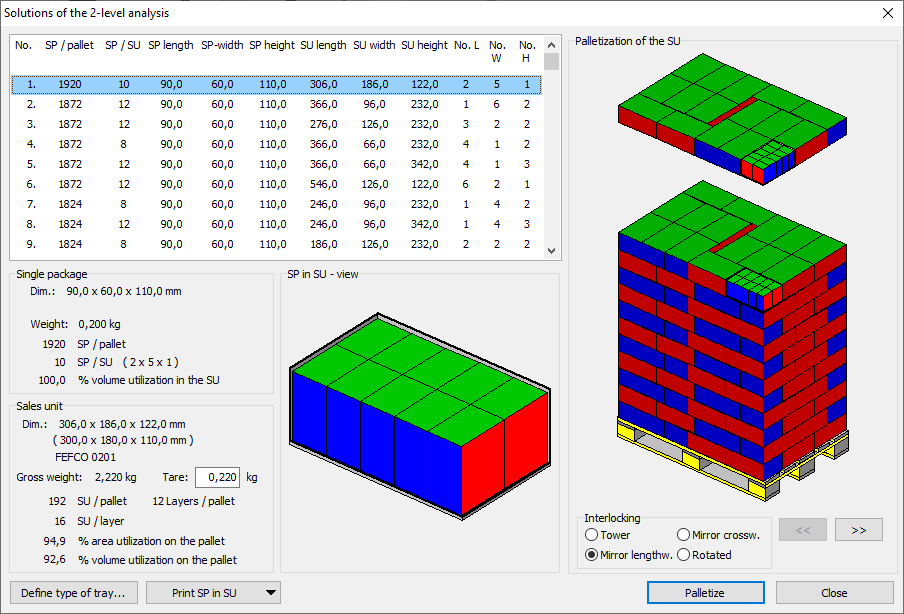
Solution report from MultiPack two-stage analysis: Pallet-compatible outer packaging with optimized number of products per outer packaging
Powerful MultiPack functions ensure an effective analysis and planning process in the packaging development every time
To enable the user to thoroughly examine the selected solution, modify it if necessary, and assess its suitability based on additional criteria relevant to the particular case, MultiPack provides further analysis and planning functions. The two-stage analysis gives the user the options of
- manually changing a layer pattern by moving, deleting, or adding outer packagings
- in the case of composite stacking, analyzing and determining alternative mirroring of the individual layers to achieve a better result from the user’s point of view
- combining different layer plans to form a stowage plan if it is not possible with mirroring or rotation of a layer plan to achieve acceptable composite stacking (top in the adjacent graphic)
- using a top layer with a different vertical orientation of the outer packaging for better height utilization of the storage space on the pallet (center in the adjacent graphic)
- analyzing layer top views, also with visible pallet slats, and all side views in order to evaluate a stowing plan in layers
- analyzing interlocking stowing plans, i.e. stowing plans not in layers (bottom in the adjacent graphic) if palletization in layers produces an unsatisfactory pallet volume utilization
- examining the assembly of the pallet load in up to four steps in order to evaluate a 3-dimensional interlocking stowing plan
- planning all load securing measures: use of slipsheets, securing straps, lids or frames and edge protection elements (bottom in the adjacent graphic)
- generating standard or customer-specific packing instructions for the solution adopted
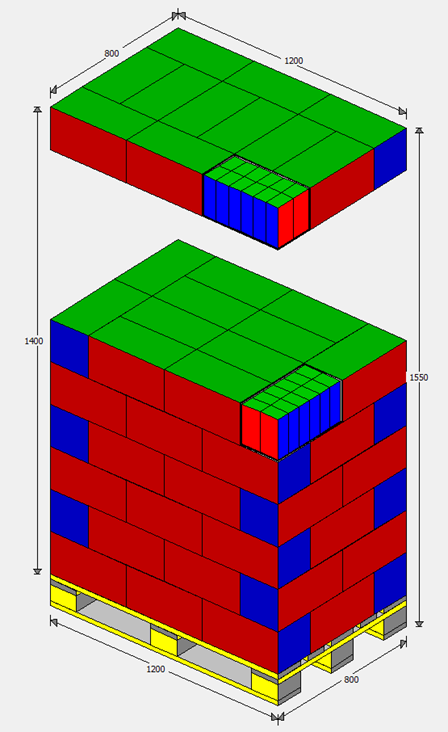
Composite stacking combining two different optimal layer plans
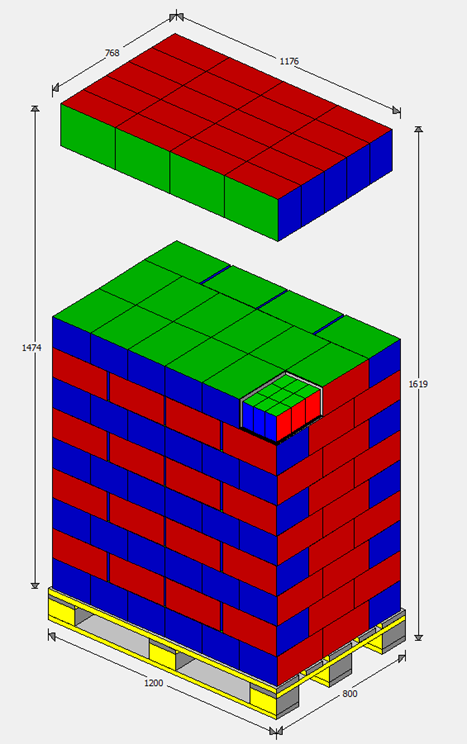
Improved utilization of pallet height by using a top layer with a different vertical orientation of the outer packaging
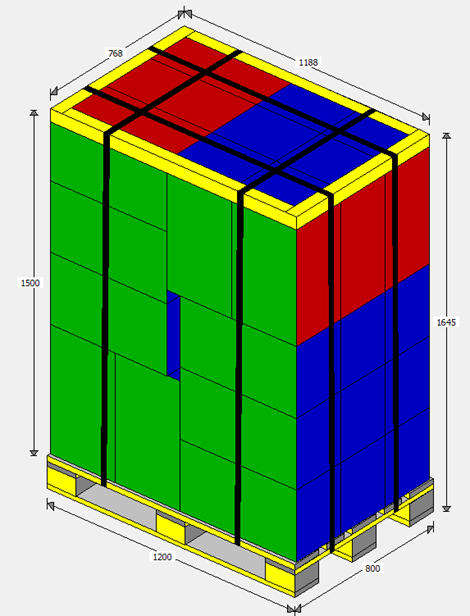
Palletization of outer packagings without layering with planned load securing
Maximization of pallet utilization with optimized vertical orientation of the products in the outer packaging
The dimensions of the product packaging may not be changed, the number of products per outer packaging is fixed, and the function of the outer packaging is purely for transport. The original plan was to place the rectangular product packages vertically by height in the outer packaging, however this results in unsatisfactory utilization of the storage space on the pallet. Is it possible to better utilize the storage space on the pallet with a different vertical orientation?
The rectangular product with the dimensions L = 85 mm, W = 60 mm and H = 105 mm is packed in bundles of 12 products in the outer packaging with FEFCO code 0201 and material thickness 2 mm. If the 12 products are packed vertically by height in the tailor-made outer packaging and the stacking height is 1,500 mm, a total of 1,944 products in 162 outer cartons can be placed on the euro-pallet in a tower-stack formation.
Is it possible with a different vertical orientation of the product in the outer packaging to improve the pallet utilization so that fewer pallets are required? MultiPack delivers the answer in fractions of a second. The adjacent solution report reveals that a vertical orientation by length and the arrangement of the products in the outer packaging shown here result in the best possible euro-pallet utilization with composite stacking: 2,304 products per pallet, which is 18.5% more than the original solution No. 8 in the list of solutions. If the products are placed in the outer packaging with a vertical orientation by width, the outer packaging shown at No. 5 in the list of solutions produces the best packaging solution, however with only 2,100 products per euro-pallet.
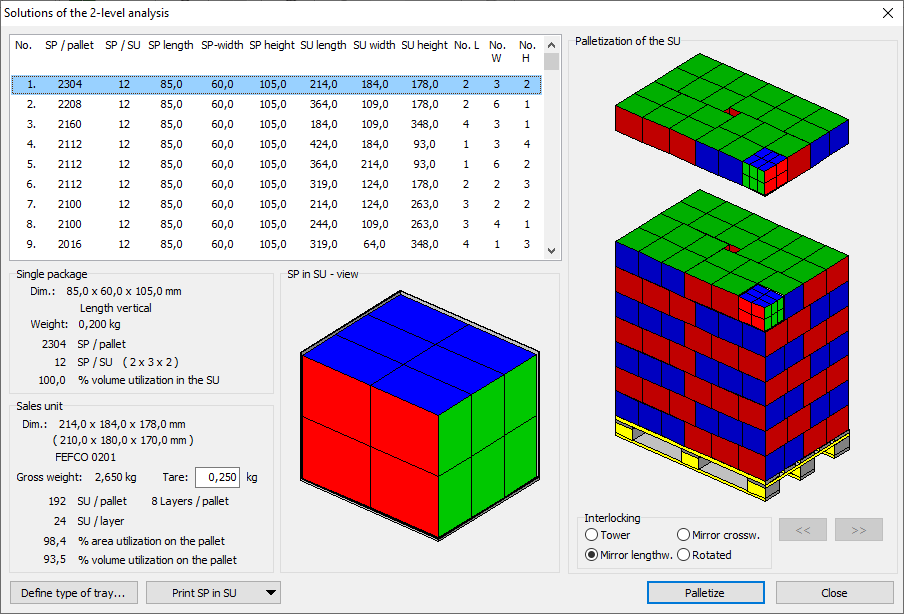
Optimized vertical orientation of products in the outer carton: The pallet utilization increases from 1,944 to 2,304 products per pallet
Circular cylindrical products are usually placed in the outer packaging either vertically or horizontally. If the user envisages either vertical or horizontal placement of the products in the outer carton, he can compare the optimal solutions for the two alternatives. In the following example, 8 products must be placed in an outer packaging with pallet-compatible dimensions. If the products are packed vertically, this results in 960 products per pallet. Horizontal placement of the 8 products in the outer packaging makes 1,064 products per pallet possible. This represents an approx. 11% better utilization of the storage space on the pallet so that every tenth pallet can be dispensed with in storage and during transport. The following graphic shows the optimal packaging solutions for the two packaging alternatives considered here.

Optimized vertical orientation of the circular cylindrical products inside the outer carton improves utilization of the storage space on the pallet from 960 to 1,064 products per pallet
Achieving the best possible utilization of the storage space on the pallet through innovative arrangement of the products in the outer packaging
The orthogonal arrangements of the products in the outer packaging shown so far do not always lead to the effective use of storage space on the pallet which users want. That is why the two-stage analysis from MultiPack offers users another possibility of exploiting optimization potential: Complex arrangements of the products both in tailor-made outer packaging and in standard packaging. These innovative packaging solutions are available from MultiPack for rectangular package formats and also for products in the form of oval or circular cylinders.
In the case of rectangular product packages, for every vertical product orientation permitted by the user, MultiPack also calculates packaging arrangements in the form of two or four-block arrangements inside the outer packaging. This option, particularly if standard packaging is used, enables better utilization of the storage space on the pallet than the normal single-block arrangement of products. The following example illustrates the improvement potential of complex packing patterns when standard packaging is used: Here, a smaller-volume standard carton is used, and the utilization of the storage space on the pallet is significantly improved.
The product has the dimensions L = 75 mm, W = 45 mm, H = 120 mm. 20 product packs, vertically oriented by height, must be packed in a standard packaging from the range used by one of our customers. On the left of the graphic below is an illustration of the smallest-volume standard packaging from the customer’s range with the usual single-block arrangement of the products in layers in the outer carton. If this suggested solution is implemented, 1,980 products can be packed on the pallet.
In this case, MultiPack can calculate a complex arrangement of the 20 products, here in a four-block arrangement, and suggest a different standard packaging from our customer’s range. The suggested solution shown on the right of the following graphic means that 2,200 products can be placed on the pallet. Thanks to the 11% improvement in utilization of the storage space on the pallet from this solution, the user can dispense with every tenth pallet and save significant logistics costs.
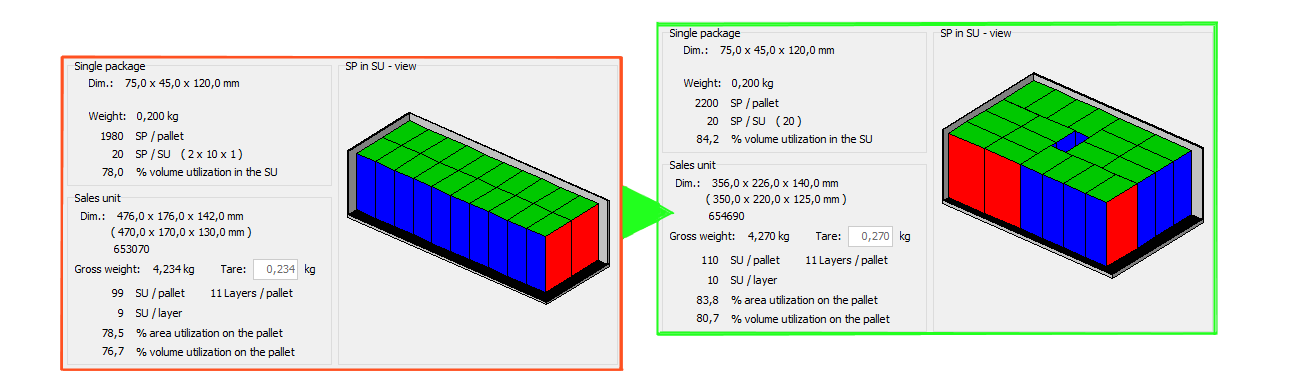
The optimized four-block arrangement of the products in the outer packaging improves pallet utilization from 1,980 to 2,200 products per pallet
The MultiPack two-stage analysis also enables our customers with circular or oval cylindrical products to determine whether and how complex product arrangements lead to better utilization of the storage space on the pallet. A product in the form of an elliptical cylinder has so far been placed in groups of 10 individual packs in an orthogonal 2 x 5 arrangement in a tray (on the left in the graphic below). The result: 630 products can be placed on a pallet. The rate of utilization of the pallet volume is 81%. Can a different arrangement of the products in the tray improve the pallet utilization? The MultiPack optimization algorithms calculate a suggested solution for this complex task in fractions of a second: With a slightly altered alignment of the 10 products in the outer packaging (on the right in the graphic below), the outer packaging can be ideally dimensioned and the utilization of the storage space on the pallet greatly improved: 700 instead of 630 products per pallet. In other words: By applying the solution calculated by MultiPack, the user can dispense with every tenth pallet in the warehouse and for transport.
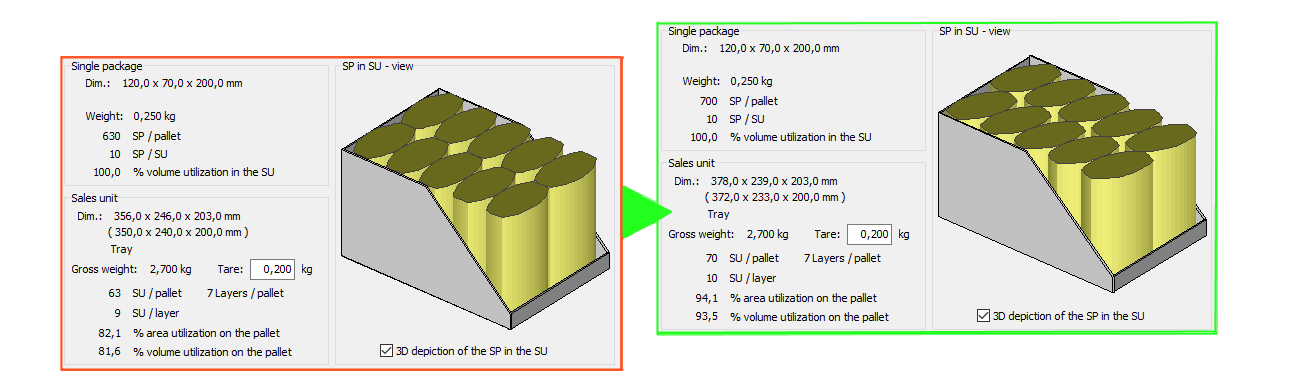
The optimized, non-orthogonal alignment of the 10 products in the tray improves the utilization of the storage space on the pallet from 630 to 700 products per pallet
Also when it comes to circular cylindrical product packagings, a complex arrangement of the products in the outer packaging often results in better pallet capacity utilization. This applies whether tailor-made or standard packaging is used. The two-stage analysis from MultiPack indicates within seconds whether there is a savings potential and, if yes, the extent of the saving. Below is an example of the savings potential that can be achieved by a complex arrangement of 20 cans placed in a single layer in a tailor-made outer packaging. If the products are arranged orthogonally in the outer packaging, it is possible with an optimally dimensioned outer packaging to place 1,440 products on the pallet (on the left in the adjacent graphic). The interlocking arrangement of the 20 products in the tailor-made outer packaging calculated by MultiPack (on the right in the adjacent graphic) results in a significantly better utilization of the storage space on the pallet: Now 1,680 products can be placed on the pallet. In other words: If the user implements this suggested solution, every seventh pallet can be dispensed with in the warehouse and during transport.
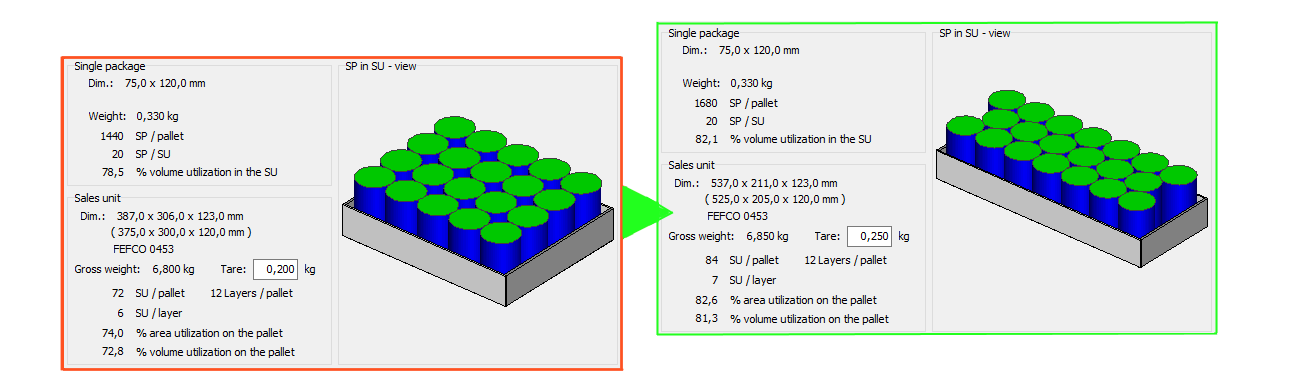
The optimized, non-orthogonal alignment of the 20 products in the tray improves the utilization of the storage space on the pallet from 1,440 to 1,680 products per pallet
Best possible utilization of the pallet with optimized number of products per outer packaging
The first example with a rectangular product packaging showed how varying the number of products per outer packaging within a range specified by the user can affect the utilization of the storage space on the pallet. Also for other individual packaging geometries, the two-stage analysis from MultiPack enables a fast and reliable examination of whether and to what extent changing the number of products per outer packaging leads to better utilization of the storage space on the pallet. In the following example, currently 12 circular cylindrical product packages are placed in an orthogonal 4 x 3 arrangement in a pallet-compatible, FEFCO 0453m tray (on the left in the graphic below). The result is that each pallet can contain 1,296 products (suggestion 2 in the solution list). As retailers also accept trays with up to 15 products, the user decides to run the MultiPack two-stage analysis to examine this option. The list of solutions generated by MultiPack in fractions of a second shows that merely increasing the length of the tray by 40 mm and packing it with 13 products in an staggered arrangement (on the right in the graphic below) produces a better pallet utilization: 1,404 instead of 1,296 products per pallet. The list of solutions also offers another fact that could be of interest to the user: Increasing the length of the tray by 86 mm and packing it with 15 products (suggested solution No. 6) results in 1,260 products per pallet, which is almost the same volume as achieved by the original solution.
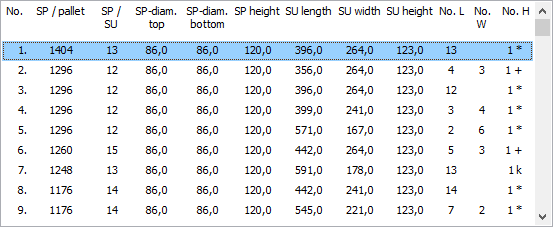
Solution list
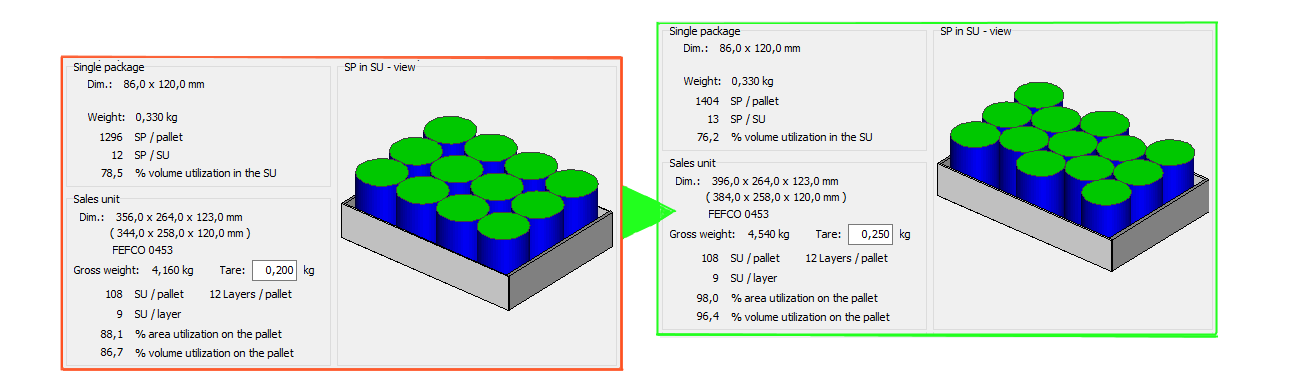
Better pallet capacity utilization with optimized number of products per outer packaging: improvement from 1,260 to 1,404 products per pallet
Using less material for the outer packaging can also significantly improve utilization of the storage space on the pallet
It may be possible to reduce the material thickness of the outer packaging by 1 mm without any loss of stability or protective function, e.g. by using corrugated cardboard with thinner liner sheets or flatter corrugations. This slightly reduces the outer dimensions of the outer packaging, which may allow a significantly better utilization of the storage space on the pallet. Here is an example: For a rectangular product, the user uses a tailor-made outer carton, FEFCO 0201, material thickness 3 mm, with the external dimensions 186 x 172 x 132 mm. Each outer carton contains 6 product packages (on the left in the graphic below). With these dimensions, a maximum of 24 outer cartons per layer can be placed on the pallet. Reducing the material thickness of this packing material by 1 mm reduces the external dimensions of the outer carton to 184 x 170 x 128 mm. The new dimensions of the outer packaging mean that 28 outer packagings per layer fit on the pallet (on the right in the graphic below). To see what the conditions are for similar improvements in the utilization of pallet storage space, see the MultiPack palletization catalog (https://palettierung-software.de/en/#potential).

Improvement of pallet utilization from 1,584 to 1,848 products per pallet by reducing the material thickness of the outer packaging by 1 mm
Best possible pallet utilization with optimized product dimensions
When it comes to products for final consumers, marketing aspects are the primary drivers behind the packaging design. Nevertheless, it still makes sense to use MultiPack to analyze the implications of this design for pallet utilization and if necessary to indicate potentials for improvement. Often, even minimal changes in the dimensions of the product packaging which are not or barely noticed by consumers lead to impressive improvements.
Some foodstuffs, e.g. cereals, pulses and muesli as well as other bulk goods offer great potential for pallet-compatible dimensioning of product packaging and outer packaging. Here is an example: A supplier of organic-grade pulses originally packs together 6 product packages with the dimensions L = 90 mm, W = 60 mm and H = 125 mm in trays designed to fit supermarket shelves (on the left in the graphic below). This results in 1,560 products per pallet.
Due to increased demand, retailers suggest that in future 8 products should be supplied in a shelf tray of the same width. Based on the user’s specifications for the product package dimensions, the MultiPack two-stage analysis calculates three optimal alternatives, including the following suggested solution: L = 90 mm, W = 49 mm, H = 154 mm. This packaging solution for the product and outer packaging (on the right in the graphic below) results in a better pallet utilization of approx. 10%: Now 1,728 products can be placed on the pallet with a tray of the same width, but 29 mm longer.

By optimizing the number and dimensions of the product in the tray, the pallet utilization improves from 1,560 to 1,728 products per pallet.
Determining the best possible outer packaging capacity utilization with complex arrangements of the packages
Optimal packing density in outer packagings saves time and money in transport and storage. It is often possible to improve the outer packaging capacity utilization if an alternative arrangement suggested by MultiPack is implemented instead of placing packages in a single-block layer pattern inside the outer packaging. A two or four-block arrangement, or a complex 3D arrangement may be better. For example, customers in the pharmaceutical industry use our MultiPack Folding Box Optimization add-on to calculate optimal alternative arrangements. Many pharmaceutical products are packed in small folding boxes. These are then combined into folding box bundles which are in turn packed into outer packagings. To achieve maximum packing density inside the outer packaging, the optimization algorithms of the MultiPack Folding Box Optimization module determine the best possible filling of the outer packaging in layers, both in the form of a single-block arrangement and a two or four-block arrangement. The module also calculates an optimal 3D arrangement of the folding box bundles in the outer packaging. If several different-sized standard packagings are available, the MultiPack Folding Box Optimization tool identifies the standard packaging with the best possible capacity utilization in a matter of seconds. Based on the suggestions provided by the optimization algorithms, the user can decide which solution to implement.
The following example is based on data from one of our customers in the pharmaceutical industry. The results of the optimization are illustrated in the two graphics below. If the ten-pack bundles are placed in layers in the outer packaging used, a single-block arrangement leads to 120 products, and a two-block arrangement to 140 products in the outer packaging.
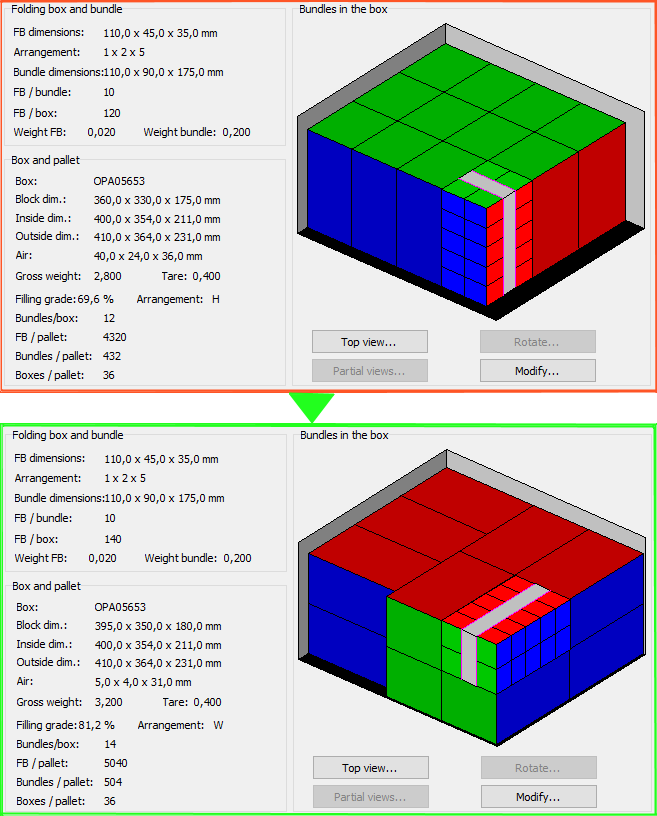
An optimized two-block arrangement in layers improves the container capacity utilization compared to an optimized single-block arrangement from 120 to 140 folding boxes
An even better outer packaging capacity utilization with 160 products can be achieved by implementing the 3D arrangement of the product bundles in the outer packaging as calculated by MultiPack (second graphic below). This typical example from practice illustrates impressively how complex arrangement patterns optimized by MultiPack lead to significant savings in logistics costs.
If the customer does not use standard packagings with pre-defined dimensions but wants to adopt an optimally dimensioned transport packaging, the three-stage analysis from MultiPack can calculate pallet-compatible transport packaging, taking into account the user’s specifications.
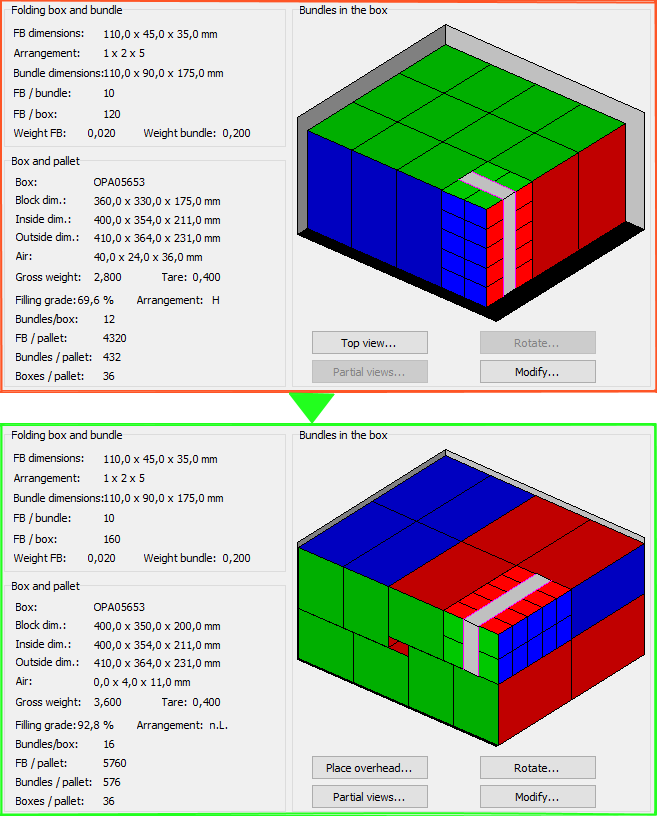
The optimized 3D arrangement of the folding boxes improves the outer packaging capacity utilization compared to an optimized single-block arrangement from 120 to 160 folding boxes per outer packaging
Packaging development of pallet-compatible outer packagings for folding box blanks
Many packaging material producers use the MultiPack two-stage analysis in the packaging development for their customers. They also use the MultiPack Blank Packaging module which we primarily developed for them. This software optimizes the dimensions of tailor-made outer packaging for folding box blanks and similar product formats with the aim of maximizing the number of blanks per pallet. If the user wants to use a standard packaging from its available range, the MultiPack Blank Packaging module selects the standard packaging that best utilizes the storage space on the pallet. If the number of blanks per outer packaging is permitted to vary within a defined range, the program module calculates the optimal quantity to best utilize the storage space on the pallet. In the following two examples, the number and arrangement of the blanks in the outer packaging is optimized in order to maximize the number of blanks per pallet.
The first example involves flat folding box blanks which the user wants to pack into the outer packaging without bundling. The aim is to determine the outer packaging that achieves the best possible utilization of the storage space on the pallet. The user specifies that each outer packaging can contain a maximum of 1,200 blanks. He enters the dimensions and permitted vertical orientation of the blanks in the outer packaging, the handling spaces (air) to be observed and the use of separators and slipsheets into the adjacent input mask. The adjacent solution report informs the user in a 3D graphic about the suggested solution that ensures the optimal utilization of the storage space on the pallet and – in the solution list – presents further solutions which could also be of interest to the user. The best possible pallet utilization is achieved when the outer packaging contains 800 blanks.
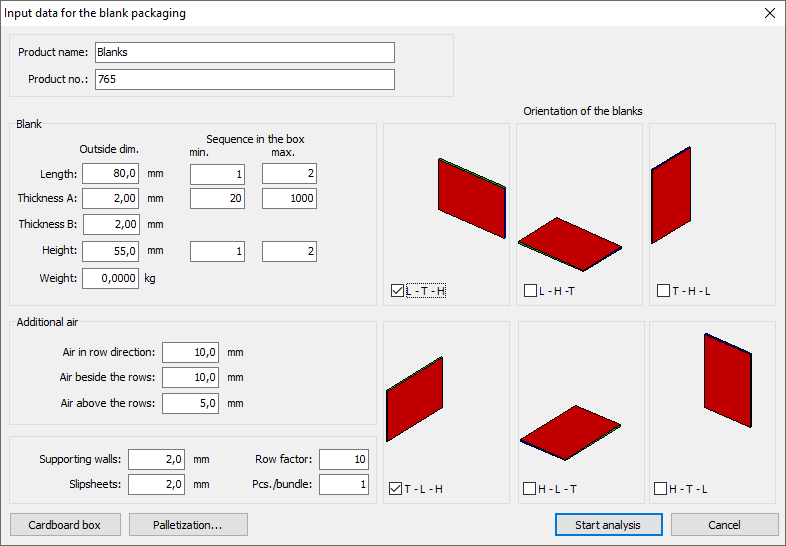
Input window for flat blanks
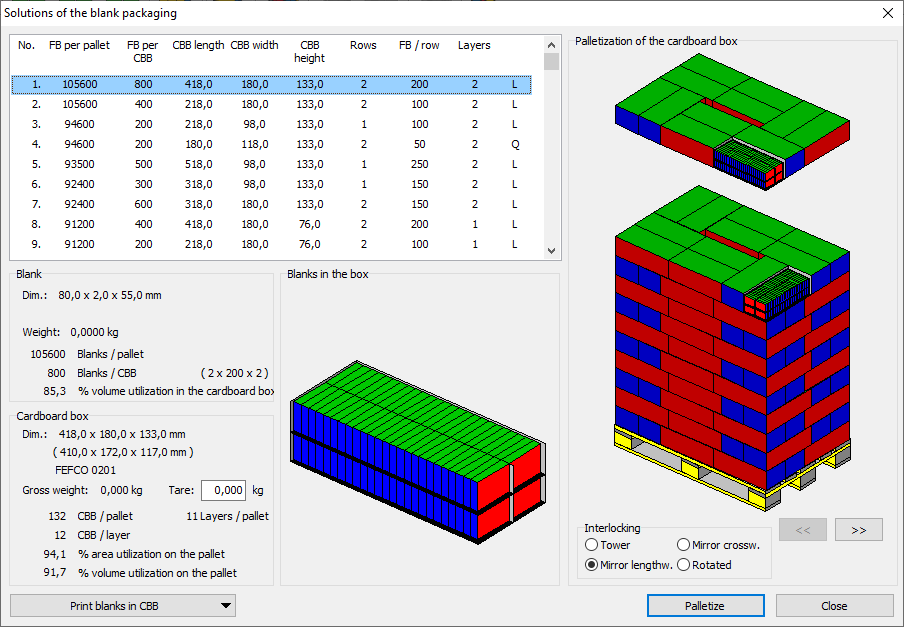
Solution report from MultiPack Box Blank module: Optimal outer packaging for flat blanks
Due to the glued edges, glued blanks have varying material thicknesses. This is why they are bundled – in the following example 10 blanks per bundle – and pairs of 2 bundles are packed in a staggered pattern in the outer carton. The aim is to determine the outer packaging that achieves the best possible utilization of the storage space on the pallet. The user specifies that each outer packaging can contain a maximum of 800 blanks. He enters the dimensions and permitted vertical orientations of the blanks in the outer packaging, the handling spaces (air) to be observed and the use of separators and slipsheets into the input mask shown on the right. The solution report shown on the right informs the user about the suggested solution that ensures the optimal utilization of the storage space on the pallet and – in the solution list – presents further solutions which could also be of interest to the user. The best possible pallet utilization is achieved when the outer packaging contains 520 blanks.
If the user requires larger folding box and carton blanks to be packed directly on the pallet, the MultiPack-Complex module generates the optimal palletization plan. (For more information, go to https://www.palettierung-software.de).
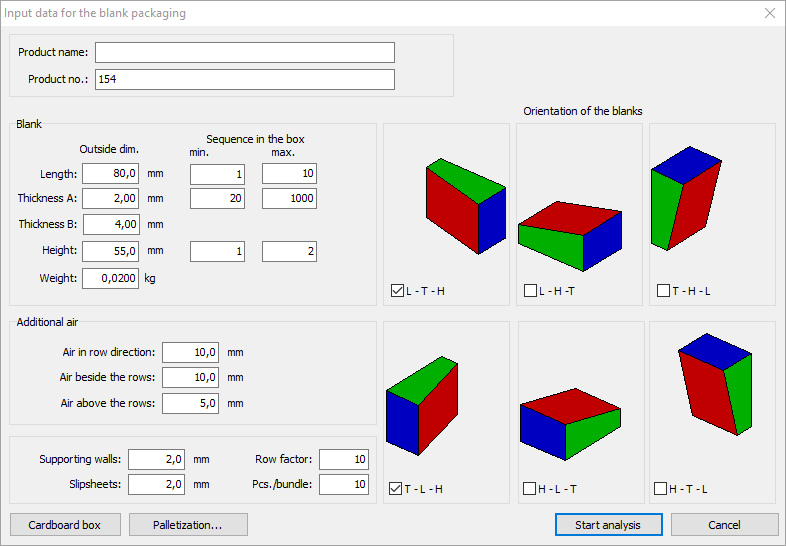
Input window for bundled glued blanks
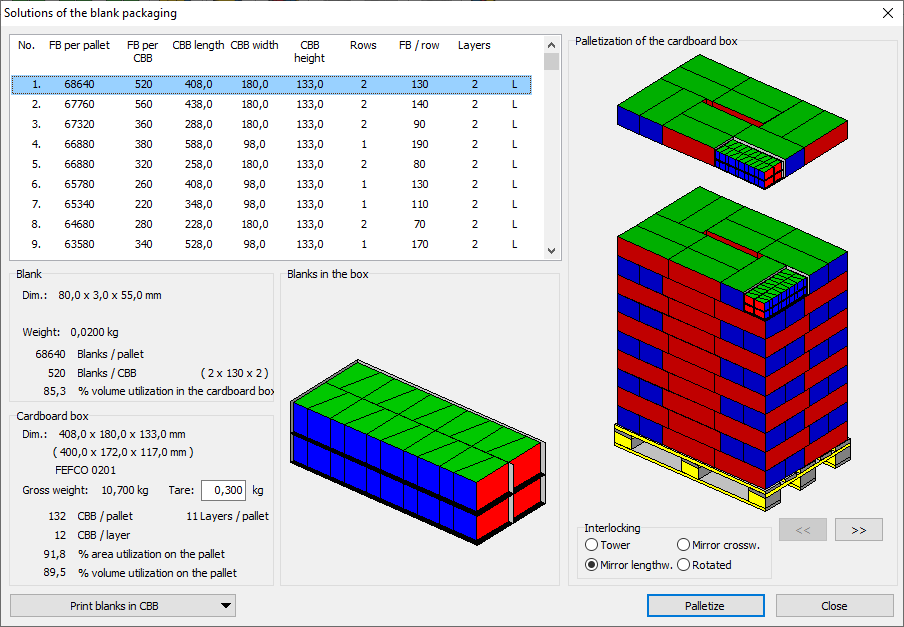
Solution report from MultiPack Box Blank module: Optimal outer packaging for bundled glued blanks
Planning the pallet-compatible outer packaging or finding the optimal standard packaging for parts with complex geometries
For parts with complex geometries such as industrial components, the two-stage analysis provided by MultiPack–Complex generates pallet-compatible packaging solutions in a matter of seconds. The user can plan both pallet-compatible outer packaging that comply with his specifications as well as determining which standard packaging from the available range offers the best capacity utilization. The primary aim is to maximize the number of complex objects per pallet.
MultiPack-Complex eliminates the need for time-consuming packing experiments which often produce unsatisfactory results. With the Multipack-Complex two-stage analysis, our customers achieve considerable logistics cost savings. MultiPack-Complex takes just seconds to calculate the best possible packaging solutions. This saves time which our customers can use for effective planning of their packing and logistics processes.
The benefits of the two-stage analysis from MultiPack-Complex
- Intuitive user interface
- Freedom to specify any load carrier dimensions (pallet, container)
- The user simply imports the contours of the complex package from his CAD file into the MultiPack-Complex module
- The user can specify the permitted arrangement structures for the complex objects in the outer packaging
- The optimization results are available within seconds
- Calculated packaging solutions as well as the associated layer and stowage plans are visualized in 3D graphics so that users can evaluate the packing results
- Additional, customer-specific functions can be integrated in MultiPack-Complex.
Planning pallet-compatible outer packagings for complex parts
The user can specify a permitted range for the number of products per outer packaging. The solution report shown here visualizes the optimization results for a customer application that requires a number of between 8 and 16 complex parts per outer packaging. The best volume utilization of the pallet, with 504 parts per pallet, is achieved with an outer packaging that contains 12 parts in an interlocking arrangement. As shown in the solution list of the adjacent solution report, MultiPack-Complex has calculated three different optimal dimensions of the outer packaging. The user has chosen the second of these options, shown here. The arrangement of the complex parts in the other two optimally dimensioned outer packagings is shown in the subsequent two graphics.
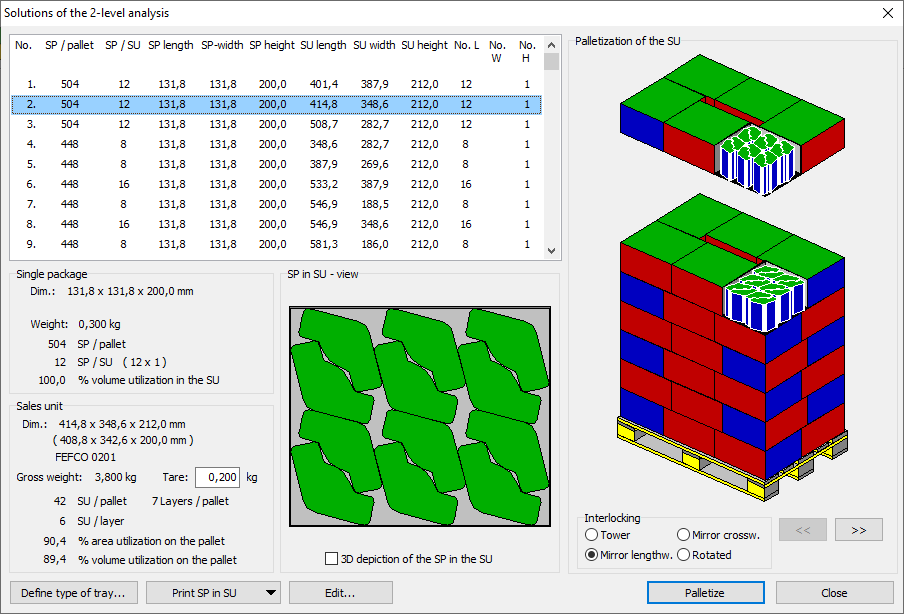
Solution report from MultiPack-Complex: Optimal outer packaging with optimized number and arrangement of the complex parts (suggested solution 2)
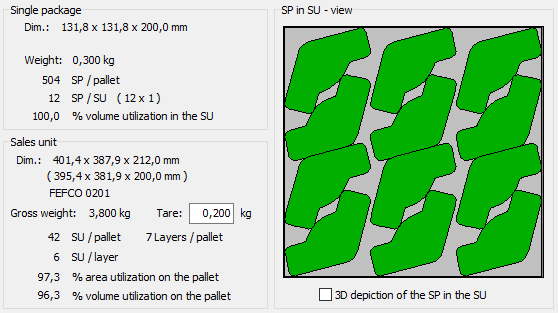
Optimal outer packaging with optimized number and arrangement of the complex parts (suggested solution 1)
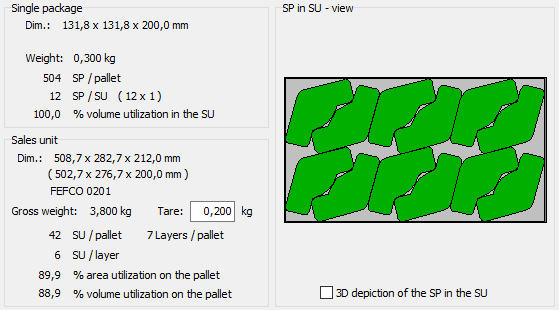
Optimal outer packaging with optimized number and arrangement of the complex parts (suggested solution 3)
Determination of the outer packaging with the best pallet space utilization for complex parts
In the following example, the user also wants to examine the potential for using already available standard packagings for the complex component shown above. The packaging to be used should contain a maximum of 20 components. Within seconds, the MultiPack-Complex optimization algorithms identify the optimal packaging: The solution is a module-compatible packaging with the outer dimensions 600 x 400 x 212 mm which can accommodate a maximum of 18 complex parts in a staggered arrangement. This solution makes it possible to place 504 parts in 28 outer packagings on the pallet. MultiPack-Complex has calculated several solutions for the arrangement of the 18 components inside the packaging. The user decides in favor of the suggested solution shown in the adjacent figure.
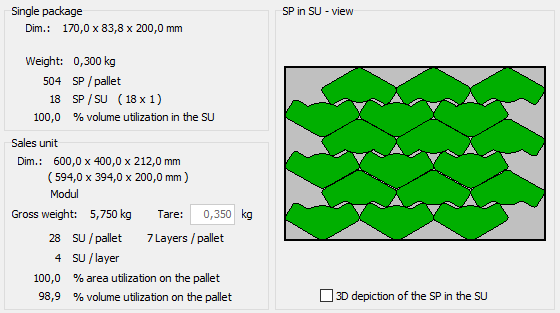
Optimal container capacity utilization through optimized number and arrangement of the complex parts
Optimal packaging development with the three-stage analysis: Overview
The three-stage analysis from MultiPack examines a three-stage packing procedure. As with the two-stage analysis, several individual packages are packed in outer packagings. However, the outer packagings are not placed directly onto the pallet. Instead, several outer packagings are packed into a transport packaging which is then palletized.
The MultiPack Three-Stage Analysis module is an extremely high-performance analysis and planning tool for the simultaneous optimal design of the individual packaging, the outer packaging and/or the transport packaging. As with the two-stage analysis, this module also takes into account the user’s specifications and calculates packaging solutions that maximize the number of products per pallet.
However, additionally the user can vary the following analysis parameters:
- Number of outer packagings per transport packaging
- Arrangement of the outer packagings in the transport packaging
- Construction and material thickness of the transport packaging
- Calculation of an optimally dimensioned transport packaging or selection of a transport container (standard packaging or returnable container) with best possible volume utilization
- Palletization of the transport packaging: either in layers as composite or tower stacking or not in layers, i.e. staggered in 3 dimensions
- Permitted packing structures of the layer plans.
Example of a three-stage analysis with MultiPack
To illustrate the use potential of the three-stage analysis from MultiPack, let’s take another look at the above example of a two-stage analysis. The product dimensions are 90 x 60 x 110 mm. The customer specifies that between 8 and 12 of these products should be packed in one layer in the outer packaging. However, the outer packaging will not be palletized. Several outer packagings, here between 4 and 6, must be placed in one or multiple layers into an optimally dimensioned transport packaging. Both options presented by MultiPack are analyzed in terms of palletization of the transport packagings: i.e. palletization in layers and palletization not in layers.
Palletization of transport packagings in layers
The algorithms of the MultiPack three-stage analysis simultaneously optimize all three packaging stages for every variation of the analysis parameters. A clearly structured solution report displays the results of the analysis, sorted in descending order of the number of individual packages per pallet. The adjacent figure shows the solution report for the task analyzed here. On the left is a list of the first 9 of a total of 31 calculated optimal solution suggestions. On the right of the window is the best pallet stowage plan for the highlighted solution suggestion, and displayed at the bottom left is information on the individual packaging, outer packaging and transport packaging as well as on the arrangement of the individual packagings in the outer packaging and the outer packagings in the transport packaging.
If the transport packagings are palletized in layers, a maximum of 1,440 products can be placed on the pallet. The volume utilization of the pallet is 76%. MultiPack has calculated a total of 31 different optimal packaging solutions which differ from each other in terms of the number of individual packagings per outer packaging and their arrangement inside the outer packaging, as well as in terms of the number of outer packagings per transport packaging and their arrangement inside the transport packaging. With the powerful analysis and planning functions provided by MultiPack, the user can examine in detail every individual solution suggestion, modify it if required and evaluate its suitability based on additional criteria relevant to the specific case.
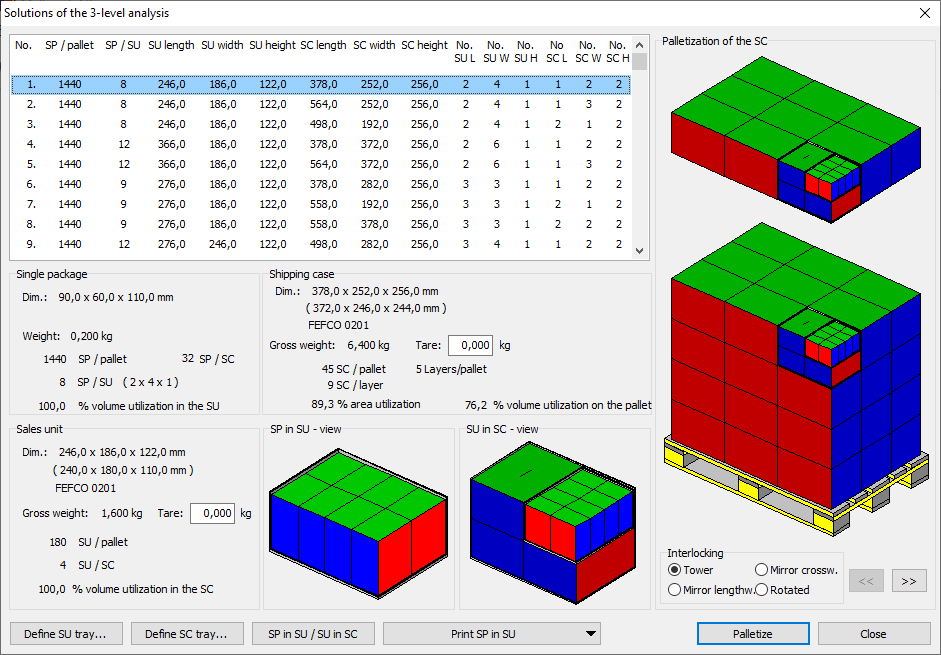
Solution report from the three-stage analysis: Optimal solution suggestion for outer packaging and transport packaging
Palletize transport packagings not in layers
In this example, palletizing the transport packagings not in layers produces a significantly better volume utilization: 1,800 products per pallet, which is 25% more than if the transport packagings were placed in layers. For this form of palletization, MultiPack has calculated three different optimal packaging solutions as well as further solution suggestions that are almost as good in terms of pallet space utilization. With the powerful analysis and planning functions provided by MultiPack, the user can examine in detail every individual solution suggestion, modify it if required and evaluate its suitability based on additional criteria relevant to the specific case.
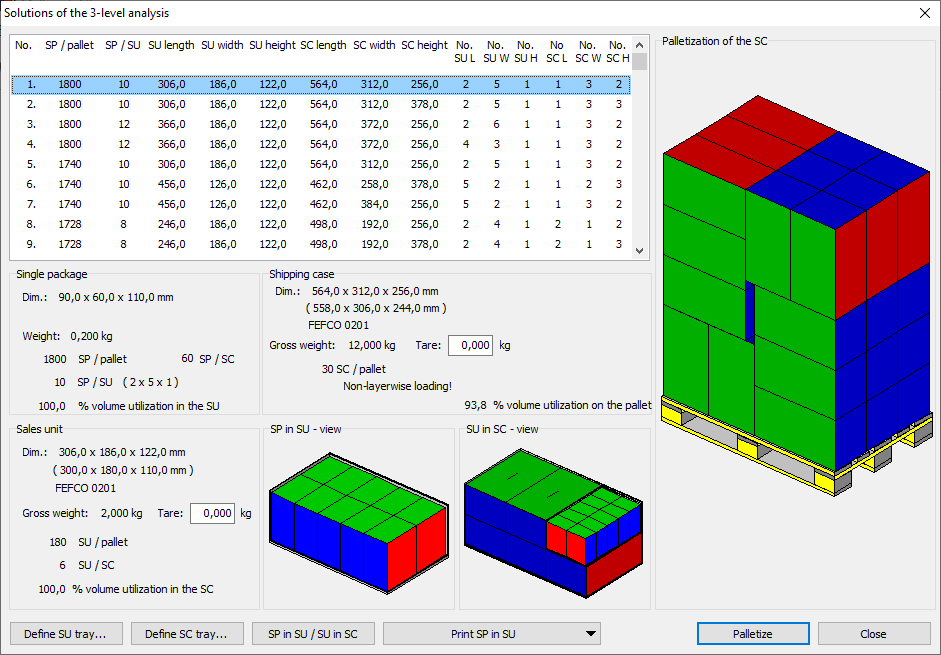
Solution report from the three-stage analysis: Optimal solution suggestion for outer packaging and transport packaging
Do you have any questions about MultiPack?
Simply contact us using the contact form or by e-mail to info@multiscience.de.
We’ll be happy to help you.